Icra’s projection is based on the EV penetration across automotive segments and its exponential growth over the next decade and battery remaining the most critical and costly component of an EV.
“In EVs, advanced chemistry batteries remain the most critical and the costliest component, accounting for almost 35-40 per cent of the vehicle price," said Shamsher Dewan, senior vice president and group Head - Corporate Ratings, Icra.
At present, battery cells are not manufactured in India, and thus most EV makers rely on imports, and manufacturing operations in India are limited to the assembly of battery packs, said Dewan.
However, to achieve mass scale penetration of EVs and a competitive cost structure, India will need to create its own ecosystem of developing battery cells locally. Multiple challenges exist on the road to establishment of a cell manufacturing ecosystem, primary ones being technology complexity, high capital intensity and raw material availability. The ability of battery manufacturers to enter into agreements/alliances with players across the value chain to mitigate these risks, coupled with the creation of a robust framework for recycling would remain critical, he said.
In addition to the robust demand from EVs, the annual battery demand for stationary applications (grid storage, telecom towers etc.) is also likely to grow at a rapid pace and be substantial, according to ICRA.
Spurred by Government support in the form of subsidies, enhanced awareness and increasing product launches, the electric vehicle (EV) segment saw a significant upturn in prospects in FY2022.
Achieving economies of scale in battery manufacturing will remain critical in lowering the cost of an EV and helping achieve pricing parity. Additionally, given that the charging infrastructure penetration will only improve gradually, improvements in energy efficiency remain imperative. Locating cell manufacturers close to the original equipment manufacturers (OEM) would allow for the creation of a research and innovation ecosystem, which would aid the development of batteries with improved energy efficiency and which are better suited to Indian climatic conditions.
Given the need to invest in cell manufacturing units to keep pace with the expected surge in battery demand for both EV and stationary applications, numerous entities have already committed significant investments in this segment. The Government of India (GoI) recently signed agreements with three companies for incentives under its Production-Linked Incentive (PLI) Scheme for Advanced Chemistry Cell (ACC) Battery Storage. The policy emphasises on enhancing domestic value addition and is expected to support capability development in this sunrise
Lithium-ion batteries have emerged as the battery of choice for EVs, given their high energy efficiency, decent thermal stability and low self-discharge. While Lithium Nickel Manganese Oxide (NMC) is the most prevalent cathode chemistry currently, Lithium Iron Phosphate (LFP) chemistry is expected to gain increased acceptance going forward, given its higher thermal stability and lower production cost. Multiple other chemistries also continue to be under development, even as commercial viability for such chemistries may take time.
One subscription. Two world-class reads.
Already subscribed? Log in
Subscribe to read the full story →
Quarterly Starter
₹900
3 Months
₹300/Month
Smart Essential
₹810
1 Year
₹67/Month
Super Saver
₹1,170
2 Years
₹48/Month
Renews automatically, cancel anytime
Here’s what’s included in our digital subscription plans
Access to Exclusive Premium Stories
Over 30 subscriber-only stories daily, handpicked by our editors
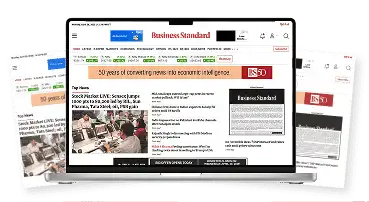
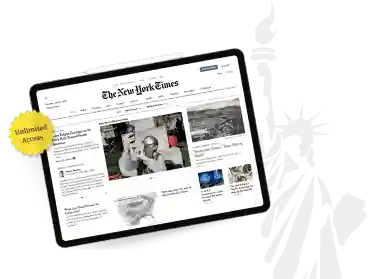
Complimentary Access to The New York Times
News, Games, Cooking, Audio, Wirecutter & The Athletic
Business Standard Epaper
Digital replica of our daily newspaper — with options to read, save, and share
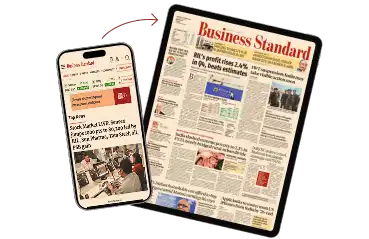
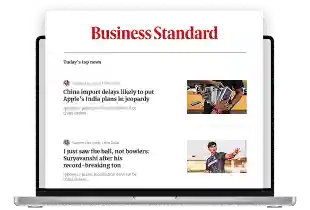
Curated Newsletters
Insights on markets, finance, politics, tech, and more delivered to your inbox
Market Analysis & Investment Insights
In-depth market analysis & insights with access to The Smart Investor
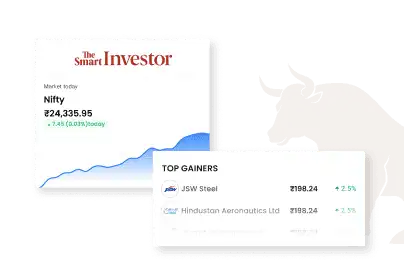
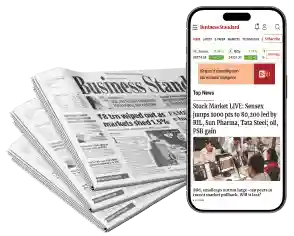
Archives
Repository of articles and publications dating back to 1997
Ad-free Reading
Uninterrupted reading experience with no advertisements
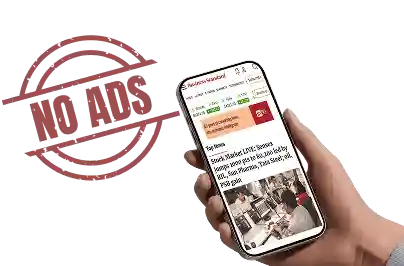
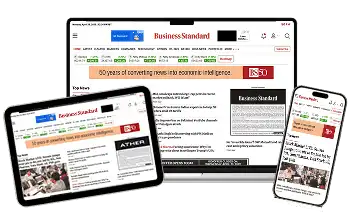
Seamless Access Across All Devices
Access Business Standard across devices — mobile, tablet, or PC, via web or app